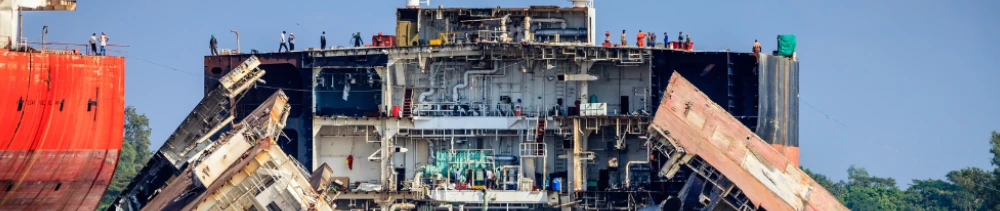
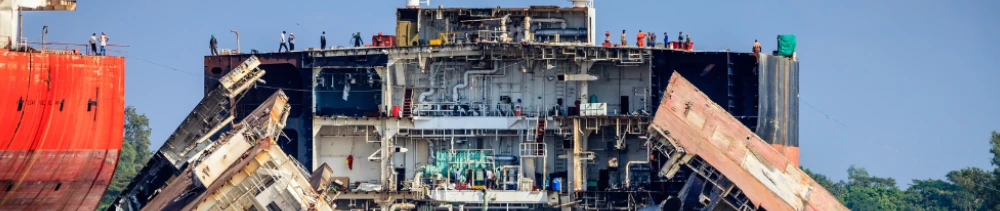
This case study highlights a high-risk asbestos removal project conducted at a ship repair site in Malibu, Africa. The project required meticulous planning, international compliance adherence, and on-site training to ensure safe asbestos identification, removal, and disposal.
This project demonstrates the importance of technical expertise, regulatory compliance, and efficient coordination in hazardous material management.
- Services
◦ Asbestos identification & abatement
◦ Hazmat handling & disposal - Industry – Shipbuilding & Repair
- Location – Malibu, Africa
- Impact – Safe removal and packaging of asbestos-containing insulation and gaskets, ensuring international compliance and risk mitigation.
The Challenges
International Coordination & Logistics
The project required mobilizing resources from India to Malibu, including sending experts for on-site assessment and risk evaluation.
Hazardous Material Handling
Asbestos-containing insulation and gaskets were widespread across the ship. Strict procedures had to be followed to prevent exposure and contamination.
Simultaneous Operations
The ship was undergoing extensive repair work with multiple contractors on site. The asbestos removal had to be isolated and controlled without disrupting ongoing repairs.
Compliance with Global Regulations
The ship’s owners mandated strict adherence to international safety and environmental regulations, including recent maritime treaties on hazardous materials.
Our Approach
Addressing these challenges required a multi-step approach, emphasizing safety, training, and regulatory compliance. (Can you please elaborate on this point? Aesthetically it would look very thin on the website otherwise)
Survey & Risk Assessment
A detailed survey was conducted to identify asbestos-containing materials. Samples were extracted, tested, and assessed for risk levels. Based on the findings, a structured abatement plan was developed.
On-Site Training & Expert Supervision
Our engineers from India travelled to Malibu and worked closely with local engineers, providing hands-on training in asbestos removal protocols and safety measures.
Containment & Controlled Removal
Given the presence of other contractors, we established restricted containment zones within the ship to prevent cross-contamination. A regulated work area was created using negative pressure systems, ensuring no asbestos fibers were released into the environment.
Strict Safety Protocols
Workers were equipped with personal protective equipment (PPE), including Tyvek suits and respiratory protection. Air monitoring was conducted throughout the process to ensure zero exposure.
Safe Packaging & Disposal Compliance
Since transporting hazardous materials across international borders was restricted, we packaged, labeled, and documented the asbestos waste before handing it over to the client for local disposal. A comprehensive custody document and inventory ensured full traceability.
Efficient Execution Within Tight Timelines
With only a one-week window and no permission for night work, we executed the project efficiently, maintaining both safety and schedule integrity.
Project Outcome
The project successfully achieved the following
Complete Asbestos Removal
All identified asbestos-containing materials, including insulation and gaskets, were safely removed and prepared for disposal.
Worker & Environmental Safety
Through rigorous containment and PPE protocols, we ensured zero asbestos exposure to workers and other personnel on site.
Regulatory Compliance & Documentation
The project met all international safety standards, including Rotterdam and Hong Kong Conventions, ensuring compliance with maritime hazardous material regulations.
Knowledge Transfer & Training
Local engineers were trained in asbestos identification and safe handling, equipping them with the skills for future maintenance and monitoring.
Global Impact: The Future of Asbestos in Shipbuilding
While older ships still contain significant asbestos materials, international treaties now mandate identification, monitoring, and removal of hazardous substances. Many countries are phasing out asbestos use in new ship construction, though exceptions still exist in some regions. Safe removal and disposal continue to be a priority for maritime safety and environmental protection.
Through projects like this, we contribute to safer working environments, regulatory compliance, and long-term sustainability in global ship repair and maintenance.
Other Case Studies
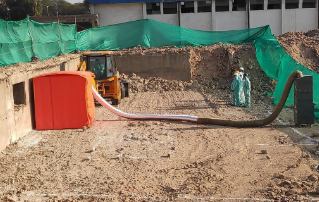
Comprehensive Hazardous Material Remediation at a Manufacturing Plant
This case study highlights a complex cleanup project at an old manufacturing plant in North India. The plant was set to be demolished.
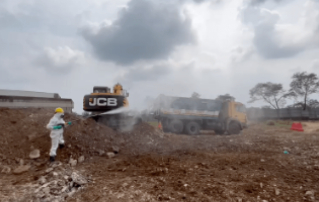
Asbestos Contaminated Soil Remediation for IT Redevelopment Project
This case study details the challenges and successful execution of a project involving the removal of 20,000 metric tons of asbestos-contaminated soil.
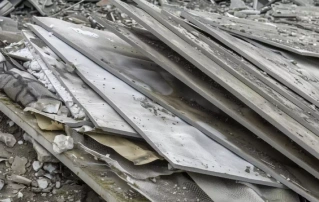
Comprehensive Asbestos Remediation at an International School
This case study highlights a critical asbestos removal project at an international school. The school management wanted to ensure a safe environment by identifying and eliminating.